2023.07.19
⾦属加⼯の種類② さまざまな⽬的に応じた付加加⼯
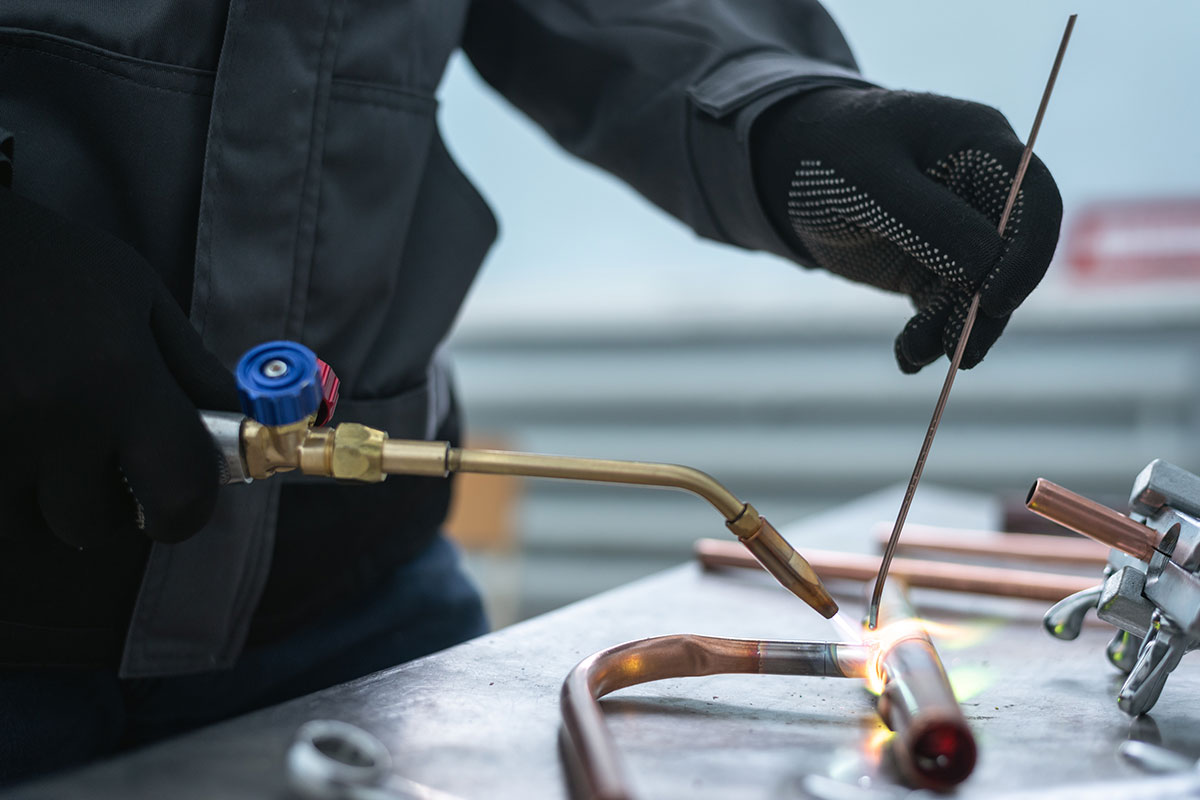
「KYOWAの⾦属加⼯ジャーナル」へ、ようこそ!
私たちは、銅加⼯・⾦属加⼯で約100年の歴史をもつ共和電機⼯業です。
「KYOWAの⾦属加⼯ジャーナル」と題したこのコーナーでは、銅をはじめ⼯業製品に⽤いられる各種の⾦属材料や加⼯法について、また⾦属加⼯の図⾯の基礎知識などもお伝えしていきます。
今回は前回からの続きで、「金属加工の主な種類」のうち、二次的な金属加工を中心に解説します。
前回は、⾦属材料から「製品(部品)の形を作る⾦属加⼯」についてご紹介しました。
前回の記事はこちら
今回は、「加⼯品に対する付加加⼯」と「⾦属の性質を調整する加⼯」をご紹介します。
代表的な⾦属加⼯の種類 | ||
---|---|---|
製品(部品)の形を作る⾦属加⼯ | ||
⾦属を削って形作る | 除去加⼯ (切削加⼯) |
旋盤加⼯ |
フライス加⼯ | ||
⾦属に⼒を加えて形作る | 成形加⼯ (塑性加⼯) |
プレス加⼯ |
加⼯品に対する付加加⼯ | ||
加⼯品を接合する | 接合加⼯ | 溶接 |
ロウ付け | ||
半⽥付け | ||
加⼯品を被覆する | 表⾯処理 | メッキ |
アルマイト | ||
その他 (仕上げなど) |
汚れ除去 ・下地処理他 |
ショットブラスト |
バリ ・カエリ除去 |
バレル加⼯ | |
酸化被膜除去 | 酸処理 (酸洗い) |
|
⾦属の性質を調整する加⼯ | ||
⾦属を硬くする ・柔らかくする |
熱処理 | 焼⼊れ &焼戻し |
焼ならし ・焼なまし |
もくじ
加工品に対する付加加工
前回ご紹介した切削加工やプレス加工は「一次加工」、一次加工の後で行う付加加工は「二次加工」に位置付けられます。
加工品を接合する「接合加工」
接合加工にはボルト&ナットやリベットなどの接合金具を用いて接合する方法もありますが、ここでは接合金具を用いずに接合する「溶接」「ロウ付け」「半田(ハンダ)付け」についてご説明します。
溶接、ロウ付け、半⽥付けの違い
溶接 | ⺟材⾃体を⾼熱で溶かして接合(融接) | |
---|---|---|
ロウ付け | 母材より融点の低い合金を接着媒体として、加熱し溶かして接合(ろう接) | ロウ剤(銀ロウなど) 融点450℃以上 |
半⽥付け | ハンダ(錫が主成分) 融点450℃未満 |
|
溶接部の強度は、溶接→ロウ付け→半⽥付けの順となります。 |
溶接
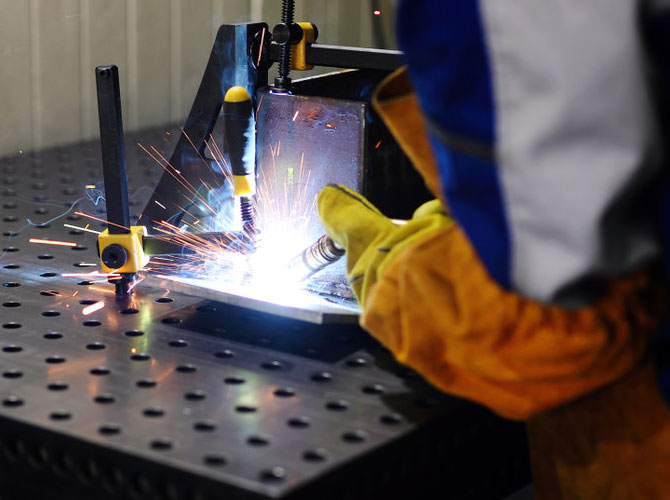
アーク溶接
接合したい金属パーツの母材そのものを高温で溶融させ(金属を液状に溶かす)急冷して結合します。
溶接のメリットは接合強度が強く接合後の気密性も高いことです。
デメリットとしては、母材が変形・変質する恐れがあることや、接合部に盛り上がりなどの溶接痕が残ることが挙げられます。
溶接方法には多くの種類がありますが、一般的に最も普及している方法は「アーク溶接」と「ガス溶接」です。
アーク溶接
アーク溶接は、「アーク放電」という放電現象を利用した溶接方法です。
溶接対象(母材)と電極(溶接棒など)に電流を流した状態で接触させて引き離すと、空気中にアーク放電が発生し、火花が散るとともに5000℃~20000℃の高熱を発します。この熱によって母材の金属を溶融します。
アーク溶接は放電を利用するため、溶接対象は基本的に電気を通しやすい金属に限定されます。
ガス溶接
ガス溶接は、可燃性ガス(アセチレンなど)を用いる溶接方法です。
ガス溶接トーチを開いて可燃性ガスに点火し、酸素ボンベで火炎を調節し、約3200℃の熱を母材の接合部に当てて溶融します。
ガス溶接はアーク溶接に比べて火花が散りにくく、溶接作業時に接合部を目視しやすい点がメリットとなります。
ガス溶接の溶接温度はアーク溶接に比べて低いため、薄板状の母材や融点の低い金属の溶接に適します。厚みのある母材の溶接にはアーク溶接の方が効率的です。
またガス溶接はアーク溶接に比べて熱が当たる範囲が広いため、局所的な溶接にはアーク溶接が向きます。
ロウ付け
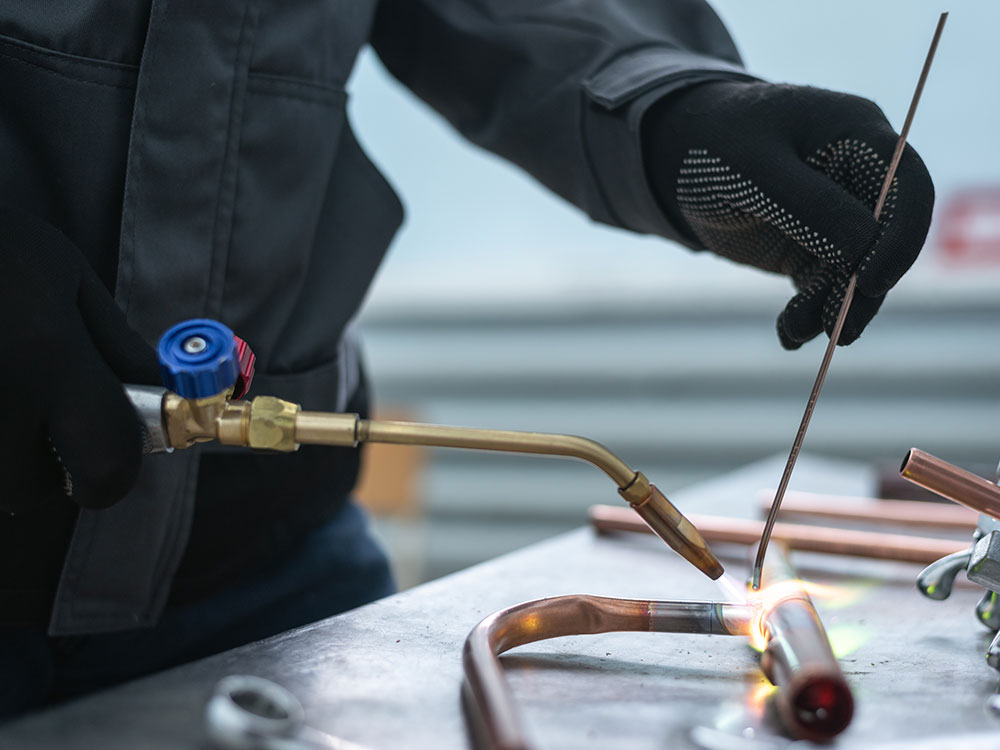
ロウ付け
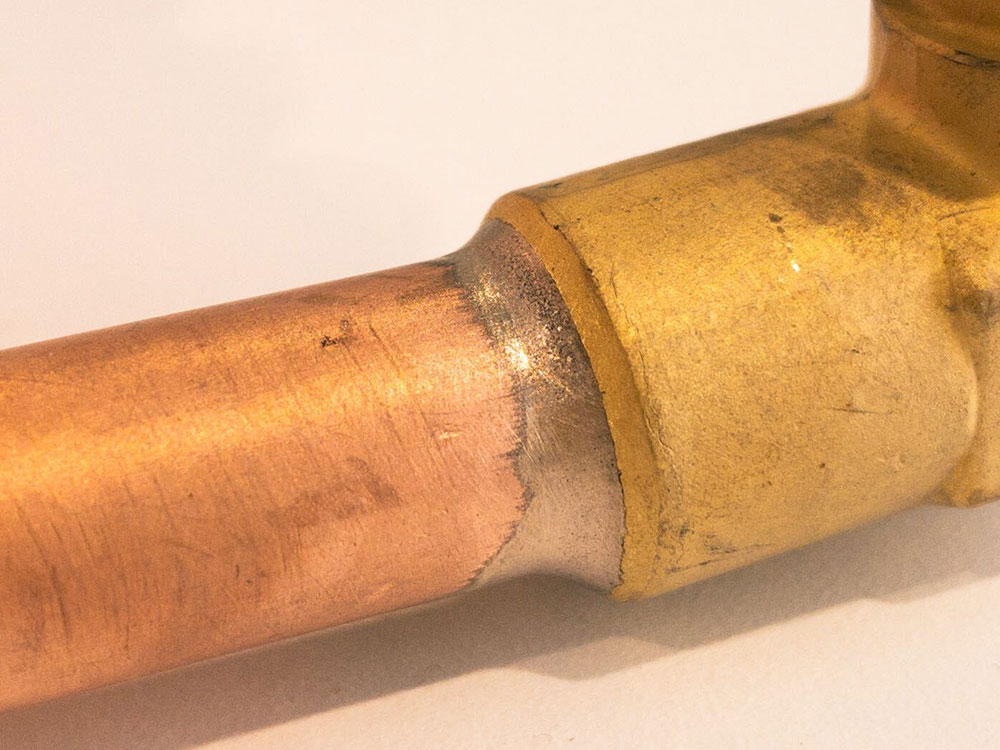
銀ロウ付けで接合した部分
「ロウ付け」「半田付け」は、いずれも母材そのものを溶かすのではなく、母材よりも融点が低い合金を接着剤のように用いて母材間を接合する方法です。
加熱して溶かした合金を母材間に行き渡らせ冷却することで、母材間に合金層が形成され接合されます。
母材はほぼ溶融しないため寸法精度が高く、溶接では困難な薄板状部品や小さな部品の接合にも適しています。
また異なる金属の接合も可能です(ただし融点によります)。
ロウ材
ロウ付けにはロウ材と呼ばれる接着媒体を使用します。
ロウ材にはさまざまな種類があり、母体の金属に応じて使い分けます。
形状も棒、板、粉、ペーストなどさまざまで、最適なロウ材を選定することが重要になります。
最も一般的なロウ材は、銀・亜鉛・銅が混ざった「銀ロウ」です。銀ロウの融点は700℃前後で、アルミニウムとマグネシウムを除き、幅広い金属に適用可能です。
弊社では銅や真鍮製品の接合加工によく用いています。
融点の低いアルミニウム(融点660℃)製品のロウ付けにはアルミロウを用いますが、母材・ロウ材ともに溶けやすいため銀ロウに比べて扱いが難しくなります。
ロウ付けのポイント「ぬれ」
母材の接合面をロウ材が伝わり広がることを「ぬれ」と言い、母材と母材の隙間全体にロウ材が行き渡るよう「ぬれ性(流動性)」を良くする必要があります。
そこで邪魔になるのが、加熱によって母材金属の表面に生成される酸化被膜です。
酸化被膜を除去するために、まず「フラックス」と呼ばれる補助剤を接合面に塗布して加熱します。フラックスは加熱し溶融することで酸化物を分解し、ロウ材のぬれ性及び毛管作用による浸透を促進する働きがあります。
このフラックスはロウ材の種類に応じて適切なものを選ばなければなりません。また多すぎず少なすぎず、適切な量を見極めることも重要になります。
「なまし」に注意が必要
フラックス及びロウ材の加熱にはガスバーナーやトーチを用いますが、フラックスやロウ材に直接炎を当てず、母材に炎を当ててその熱でフラックスやロウ材を溶かします。
※ロウ材と母材を同一の温度で加熱することがポイントとなります。
加熱によって母材そのものが溶融して変形することはほぼありませんが、加熱した面はなまされて柔らかくなります。その点で問題がないかどうかを検討する必要があります。
半田付け
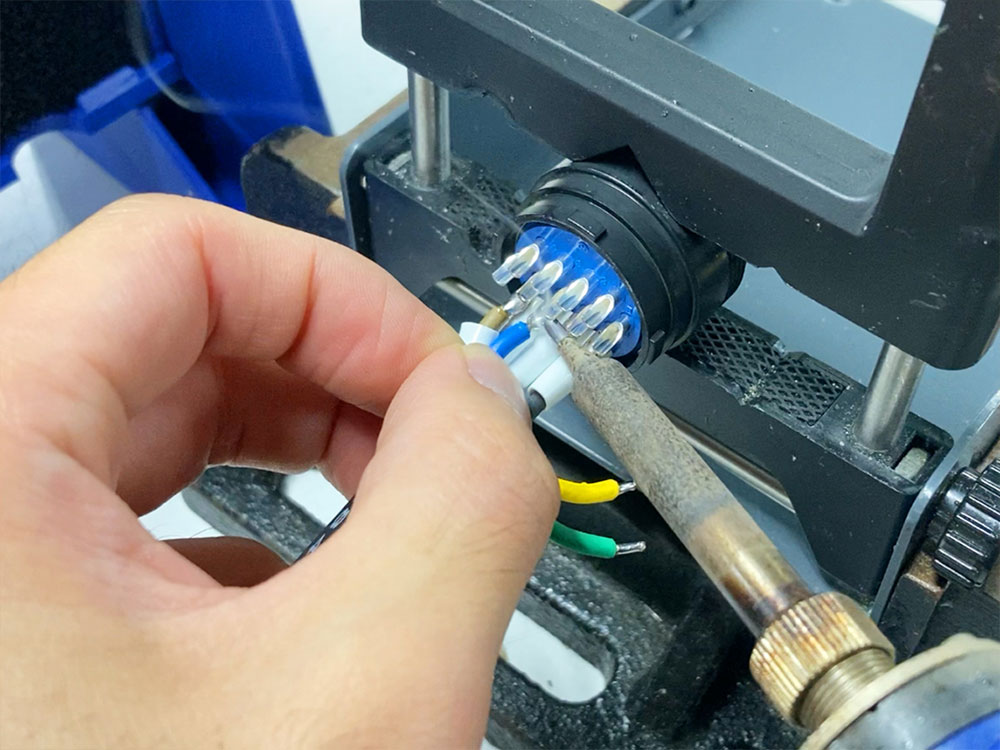
半⽥付け
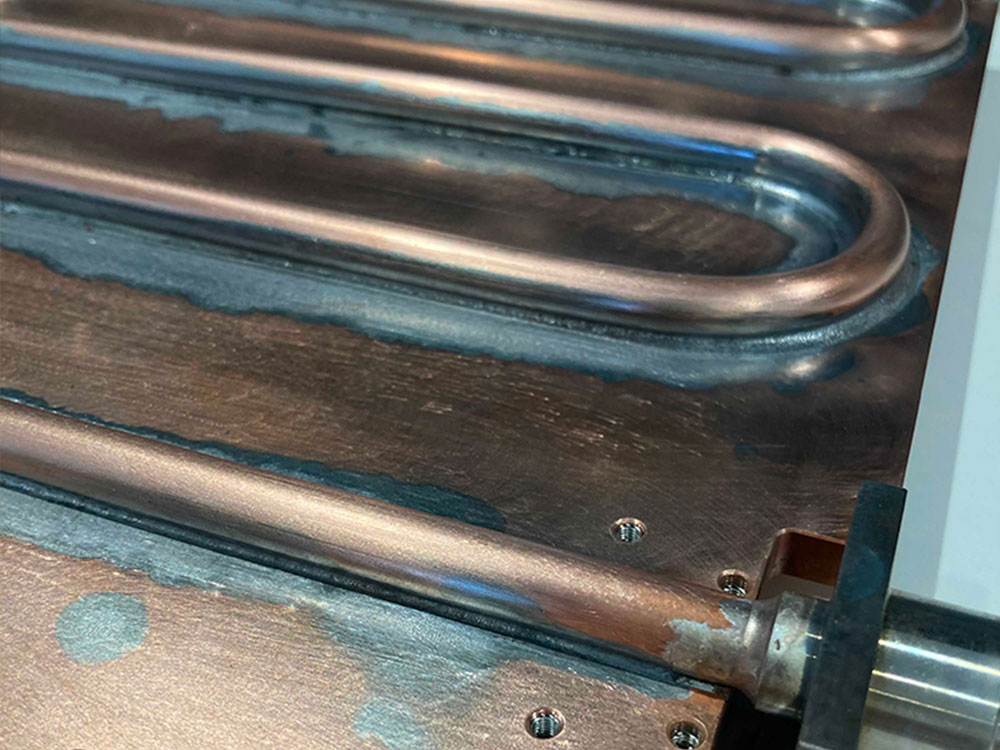
半⽥付けで接合した銅板とパイプ
半田(ハンダ)付けの接合原理はロウ付けと同じですが、接着媒体となる合金の融点で区別されています。
半田付けに使用するハンダは、錫(すず)を主成分とし、融点は450℃未満。
ロウ付けに使用するロウ材は、成分は多様ですが、融点は450℃以上。
ハンダは「軟ロウ」、ロウ材は「硬ロウ」と呼ばれることもあります。
ロウ付けによく用いる「銀ロウ」は前述したように700℃前後で溶融し、対してハンダは200℃前後で溶融します。
ロウ付けの方がより高温で加熱する必要があり、そのぶん接合強度が優れますが、母材への影響も半田付けよりは大きくなります。
また、半田付けもロウ付けと同じく接合品質において「ぬれ」が重要となりますが、半田付けの場合はハンダ合金の中心にフラックスが充填されたハンダを用いることができるため、比較的手軽です。
半田付けは細かい作業に向き、修正も容易
加熱する道具も異なり、半田付けには炎の出ない「ハンダゴテ」を用いるのが一般的です。ハンダゴテの先端をハンダに当てて溶かし、ボンドのように用いて部品同士を接合します。
ハンダゴテは先端が細くハンダも細い針金状のため、細かい作業に向きます。また接合後も再加熱により修正が容易です。
その特徴から、プリント基盤に電子部品を取り付ける際や、プラグに通電部品を取り付ける際など、細かい部品を接合して製品を組み立てる作業にはロウ付けよりも半田付けが適しています。
なお、大きめの部品についても、強固に接合する必要性がない場合は、ロウ付けよりも作業が手軽な半田付けを用いるケースがあります。
半田付けに向く金属・向かない金属
半田付けに向く母材の金属は、銅・スズ・ニッケル・真鍮など。
向かない金属はステンレス・アルミ・チタンなど。これらは半田付けでは十分な接合強度が得られません。
加⼯品を被覆する「表⾯処理」
メッキ
メッキ(鍍金)は、製品の耐⾷性(防錆など)や機能性(導電性など)を高めることを目的とし、母材金属とは異なる金属の被膜で母材表面を覆う二次加工です。
例えば、鉄は非常に錆びやすい金属であるため、必ず何らかの防錆処理がされており、三価クロメート等によるメッキ処理もその一つです。
銅製品の導電率をさらに向上させる「銀メッキ」
銅加工を得意とする弊社では、銅の導電性を活かした電力部品の製作実績が豊富ですが、さらに導電性能を高めたい場合には銅に銀メッキを施します。
銀は金属材料の中で最も導電率が高く、しかし価格は銅の10倍ほどになるため、少量で済むメッキ材料として用いることでコストを抑えて性能を向上させます。
その他、メッキ後に半田付けを行う場合は融点の低い錫メッキを施すなど、必要に応じてメッキ金属を選択します。
また母材とメッキ被膜となる金属の相性も重要で、相性が悪い場合はメッキの密着性を⾼めるために下地メッキを施した上で表⾯メッキを施します。
「錫メッキを施す場合の例」もご参照ください
電気メッキの原理
弊社では基本的に電気メッキにて対応しております。
電気メッキは湿式メッキ手法の一種で、電気によって溶液中の金属イオン(メッキ被膜となる金属のイオン)を還元し、メッキしたい製品の表面に被膜を形成させます。
メッキの中で最も種類が多く一般的な方法であり、電気を通す素材全般に適用できます。
メッキ被膜となる金属の金属イオンを含む水溶液中に、被膜となる金属とメッキを施したい金属を浸し、被膜となる金属には陽極(プラス)、メッキを施したい金属には陰極(マイナス)の電極をつないで直流電流を流します。
すると溶液中で還元反応が起こり、陰極(マイナス側)の金属の表面にメッキしたい金属が析出され金属皮膜を形成します。
アルマイト
アルマイトは、アルミニウムに対して行う表面処理です。
アルミニウムは空気中の酸素と結びついて表面に酸化被膜を生成するため、鉄に比べると錆びにくい素材ですが、柔らかく傷がつきやすい素材でもあります。
自然に生成される酸化被膜はごく薄く、傷がつくとそこから腐食してしまいます。
(傷だけでなく環境条件によって腐食する場合もあります)
そこで人工的に、厚く耐久性の高い酸化被膜を作るアルマイト処理(陽極酸化処理)を行います。
「メッキとアルマイトの違い」もご参照ください
アルマイトの原理
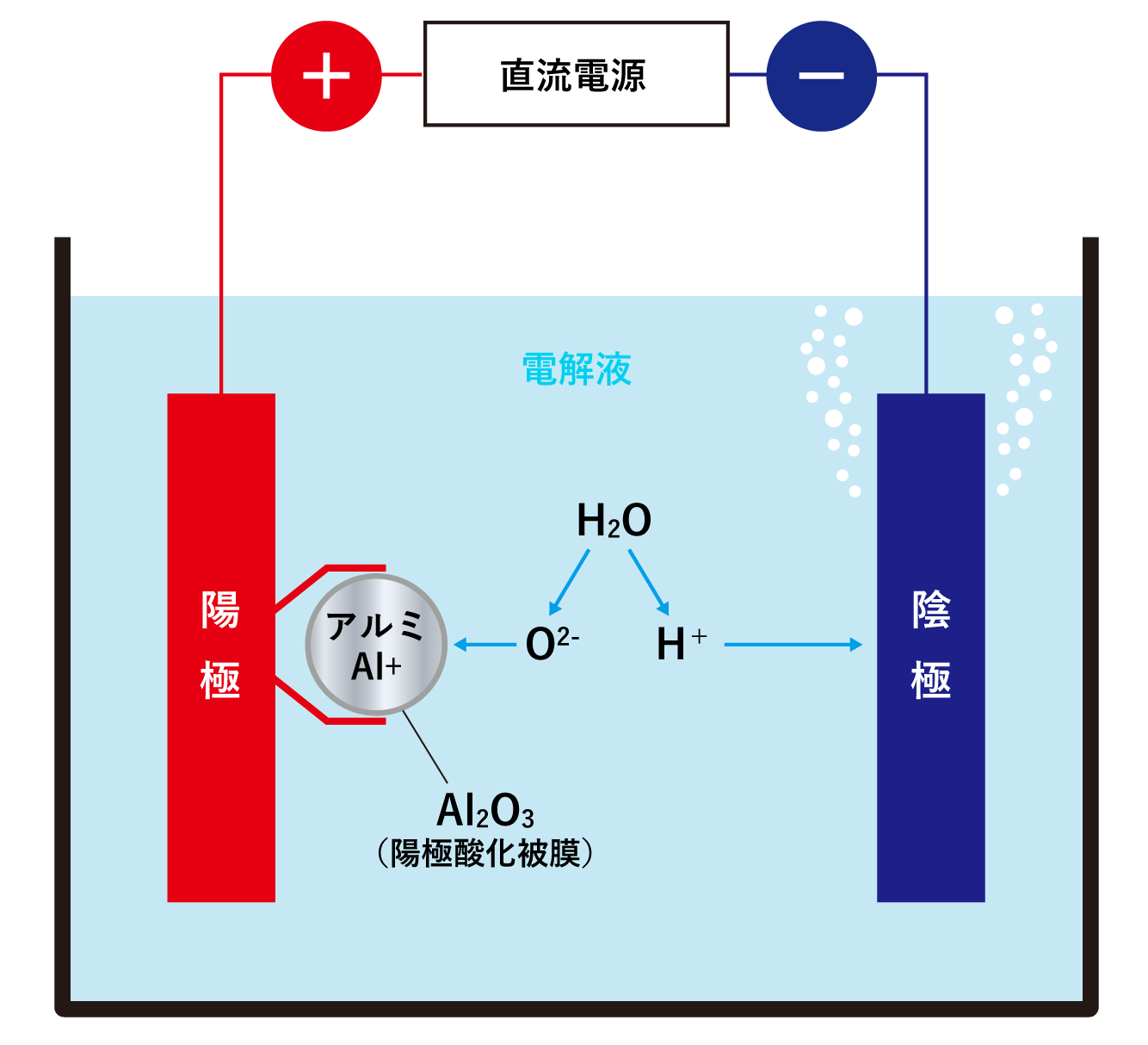
アルミニウム製品を治具にセットして電解液(硫酸やシュウ酸)に浸します。
治具に陽極(プラス)の電極をつなぎ、陽極・陰極に電流を流します。電気分解によりアルミニウム製品の表面に酸化被膜(アルミの酸化物)が形成されます。
アルマイトの特徴
①耐腐食性・耐摩耗性が向上する
アルマイト処理により耐腐食性だけでなく耐摩耗性も備わり、傷にも強くなります。
②絶縁性が備わる
アルミニウムは電気を通しますが、アルマイト処理によって生成された酸化被膜は電気を通しません。アルマイト処理を施したアルミニウムは絶縁性材料として利用できます。
③熱伝導率が低くなる
アルマイト処理を施したアルミニウムの熱伝導率は、未加工のアルミニウムの約1/3となります。また遠赤外線の放射性は高くなります。
アルマイト被膜は着⾊することも可能
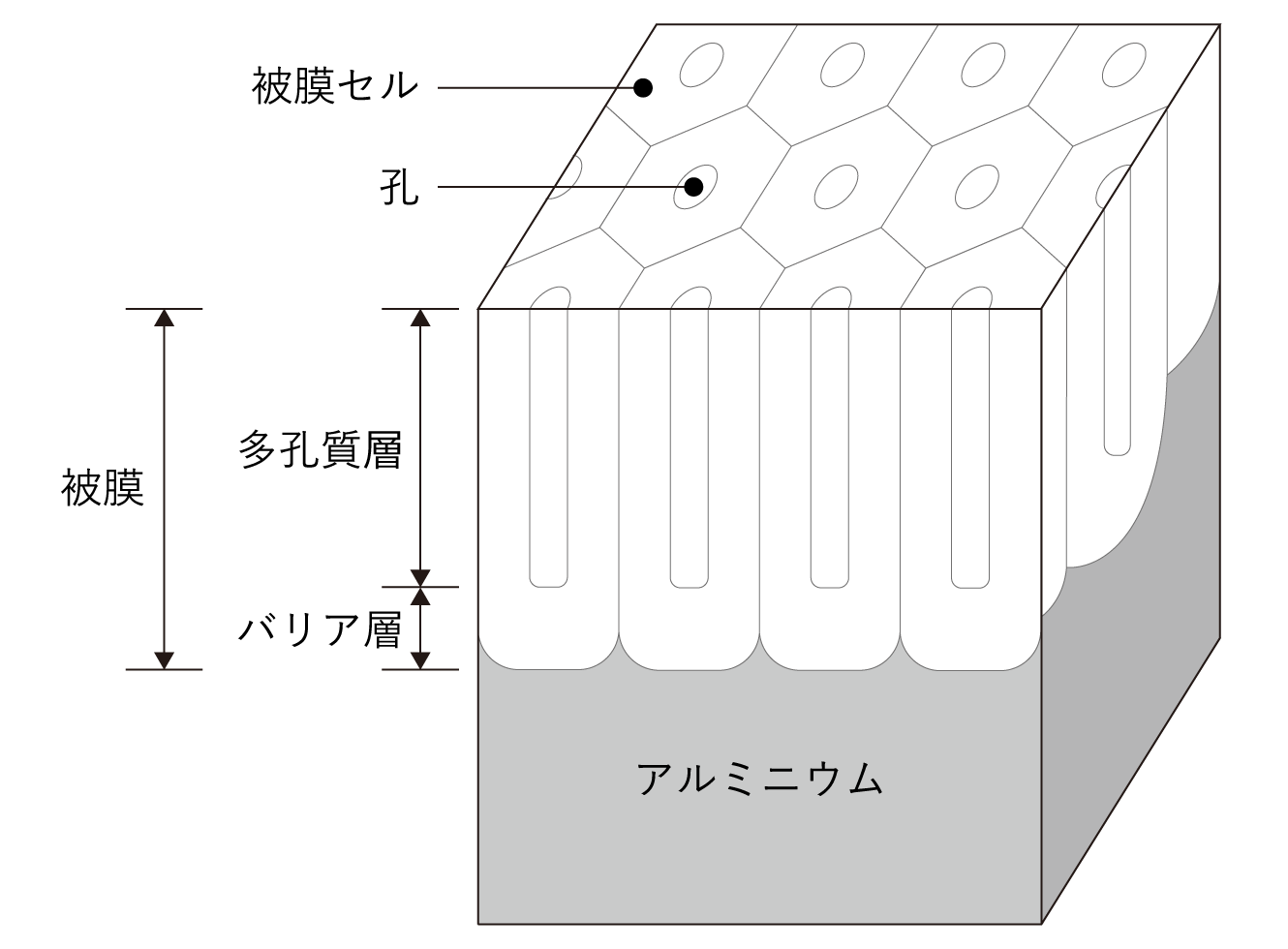
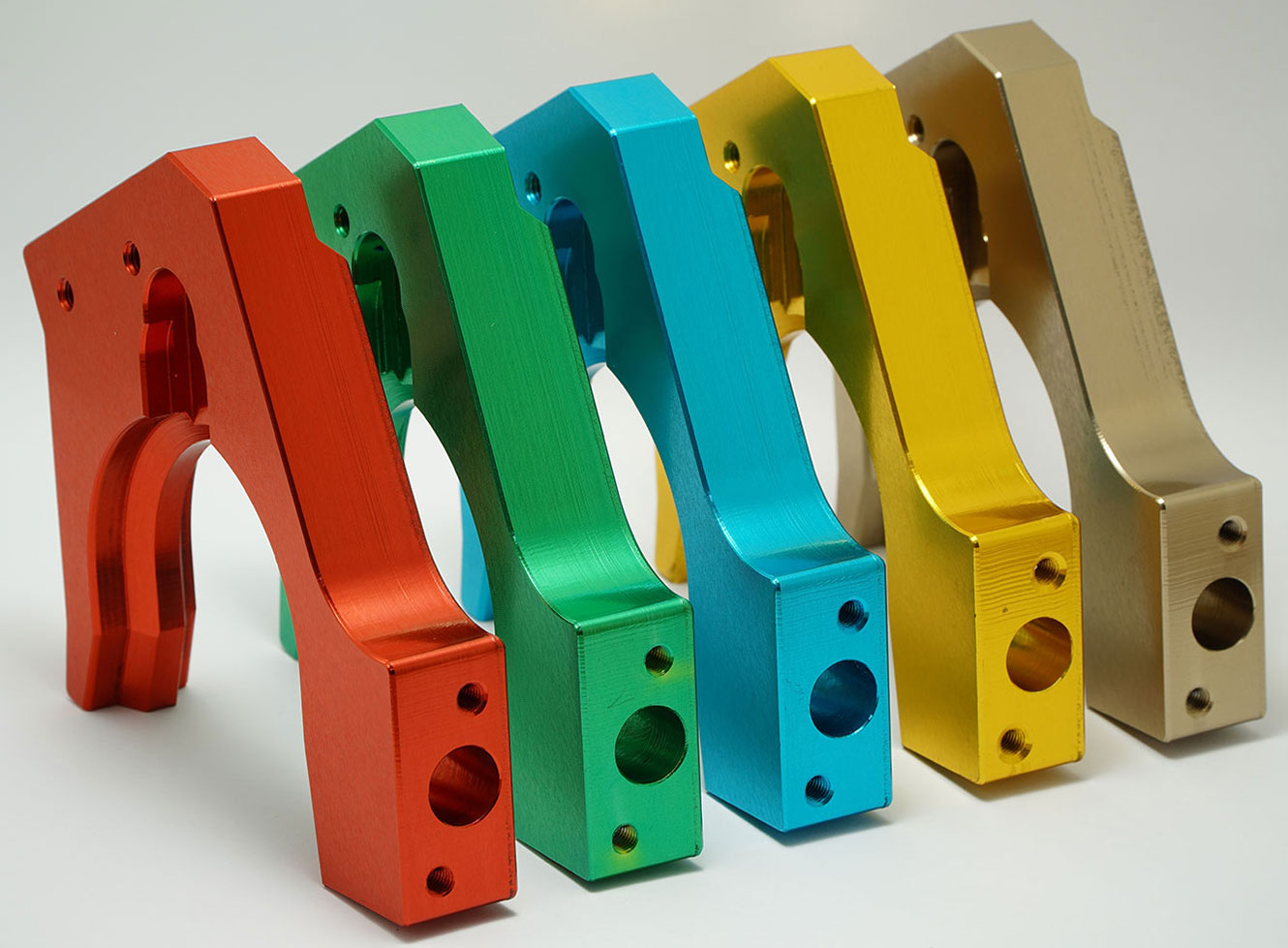
カラーアルマイト
その他、仕上げなど
各種の仕上げ加⼯については、下記のリンク先ページをご参照ください。
ショットブラスト:汚れ除去・下地処理他
バレル加工:バリ・カエリ除去
酸処理(酸洗い):酸化被膜除去
⾦属の性質を調整する加⼯
⾦属を硬くする・柔らかくする「熱処理」
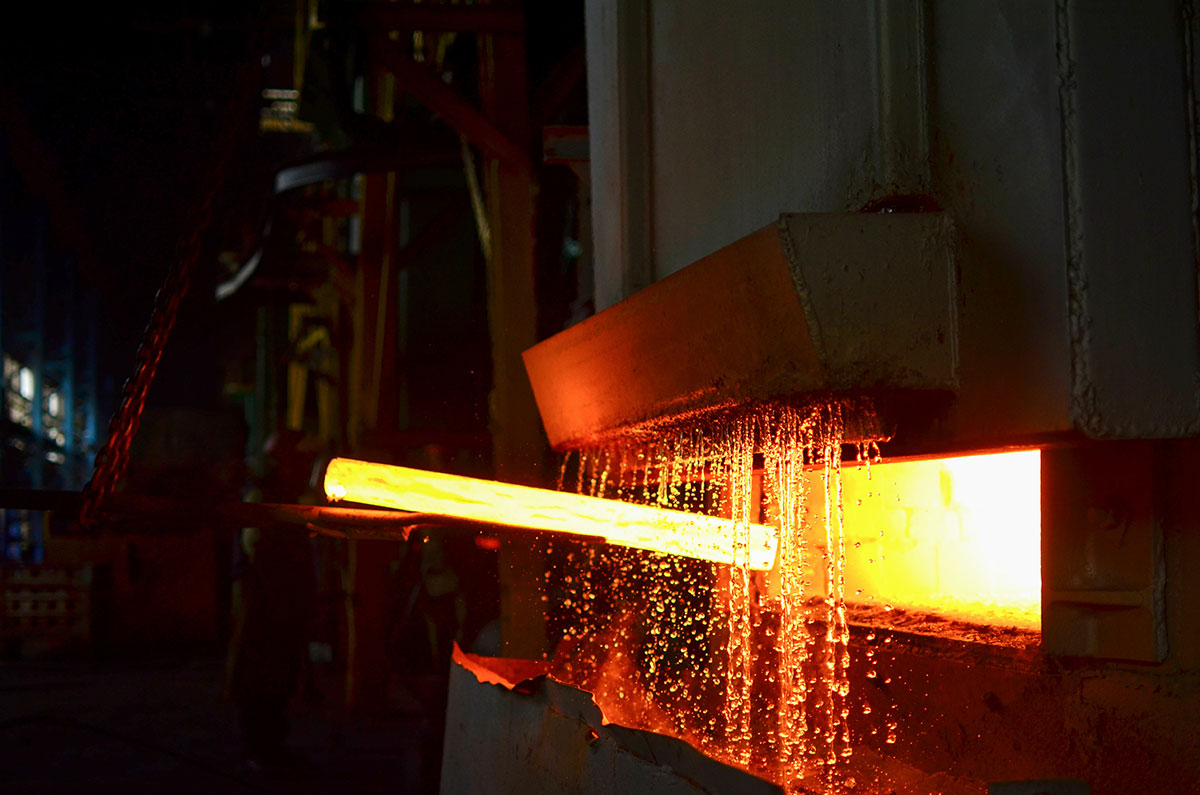
熱処理とは、炭素を含む金属(主に鋼材)に熱を加えて冷却することで生じる金属組織の変化を利用し、金属の性質や加工性を向上させる処理方法です。
熱処理の主な⽬的
①硬くする(強度や耐摩耗性を高める)
②調質(金属組織を均一にして安定させる)
③残留応力除去(機械加工や熱処理によって発生する内部応力を除去して安定させる)
熱処理の種類とそれぞれの⽬的
焼⼊れ | 硬質化・強度UP・耐食性UP・耐疲労性UP |
焼戻し | 焼入れ硬さの調節・内部応力緩和・靱性UP・靱性調節 |
焼なまし(焼鈍) | 織の軟化・切削性の向上・内部応力除去・組織改善・炭化物の球状化 |
焼ならし(焼準) | 内部応力除去・結晶組織の球状化・塑性加工組織の改善 |
焼⼊れ&焼戻し
焼⼊れ(硬くする)と焼戻し(強くする)は基本的にセット
「焼入れ」は鋼材を硬くする熱処理です。炉で800℃〜850℃に加熱した後、油や水に入れて急冷し、さらに空冷します。
加熱により鋼の組織はオーステナイト化し(鋼が柔らかくなる)、急冷によりマルテンサイト化します(鋼が硬くなる)。
焼入れによって硬くはなりますが、そのままでは衝撃に対して脆い状態です。
そこで、今度は靱性(粘り強さ)をもたせるために「焼戻し」を行います。
焼戻しも炉で加熱しますが、加熱温度は420℃、冷却は空気中でゆっくりと行います。
また、靱性よりも硬さを優先する場合は低温焼戻し(150℃〜200℃)、硬さよりも靱性を優先する場合は高温焼戻し(550℃〜650℃)を行います。
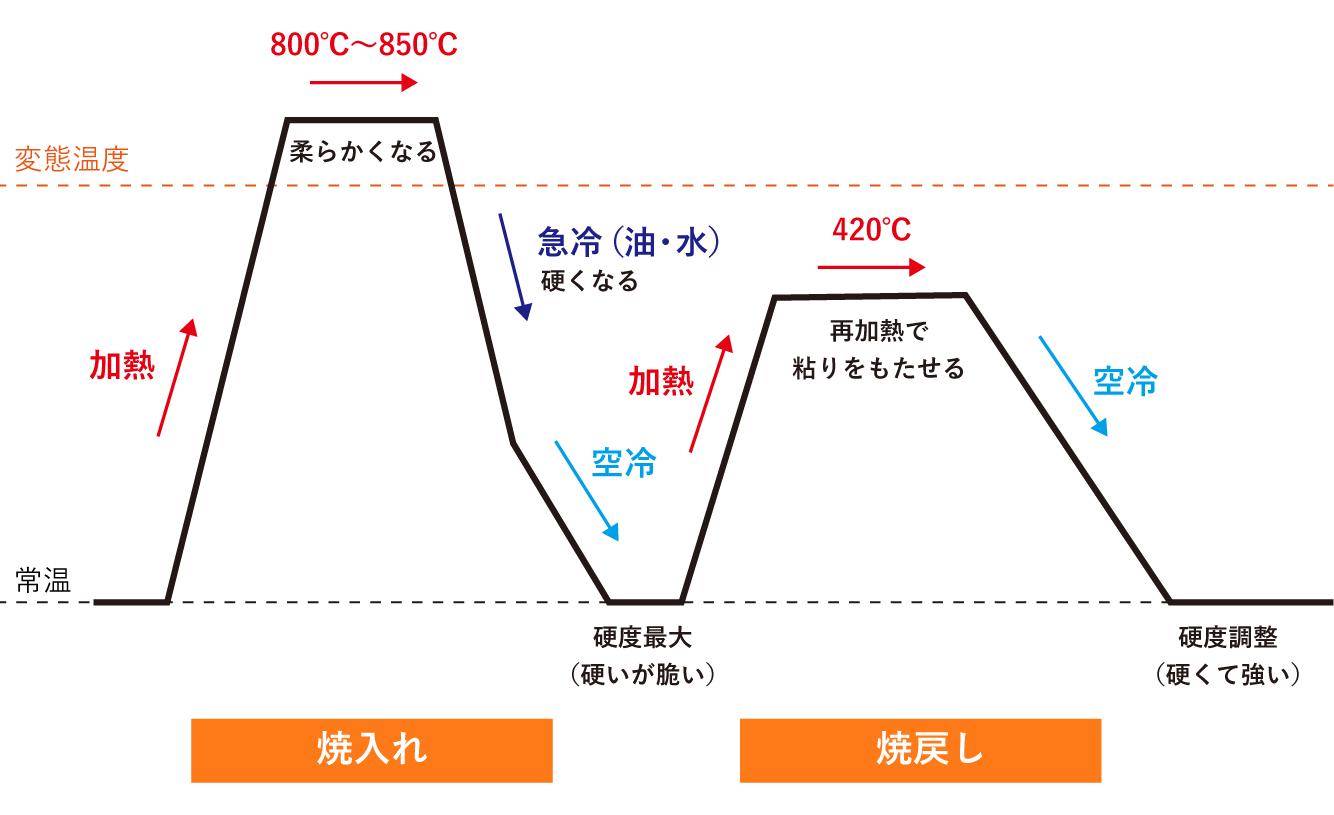
焼なまし・焼ならし
焼なましも焼ならしも、焼入れや焼戻しと同じように鋼材を加熱・冷却する熱処理ですが、鋼を硬くすることではなく柔らかくすること、組織を均一にして機械的性質を向上させることを目的とします。
また処理のタイミングも異なり、焼入れ・焼戻しは基本的に加工後に行い、焼なまし・焼ならしは基本的に加工前に行います。
焼なましは「焼鈍(しょうどん)」とも言い、
・鋼を柔らかくして切削加工やプレス加工などの加工をしやすくする
・鋼の組織を均一にして加工精度を高める
ことが主な目的です。
焼ならしは「焼準(しょうじゅん)」とも言い、
・鋼の組織を均一化し、結晶粒を微細化して引張強さなどの機械的性質を向上させる
ことが主な目的です。
いずれも細かい目的に応じた種類があり、加熱温度・時間、冷却方法などが異なってきます。
以上、今回は「さまざまな目的に応じた付加加工」について解説しました。
次回は、弊社の得意分野の一つである「可とう導体」の製造工程をお見せします。